Subscribe newsletter
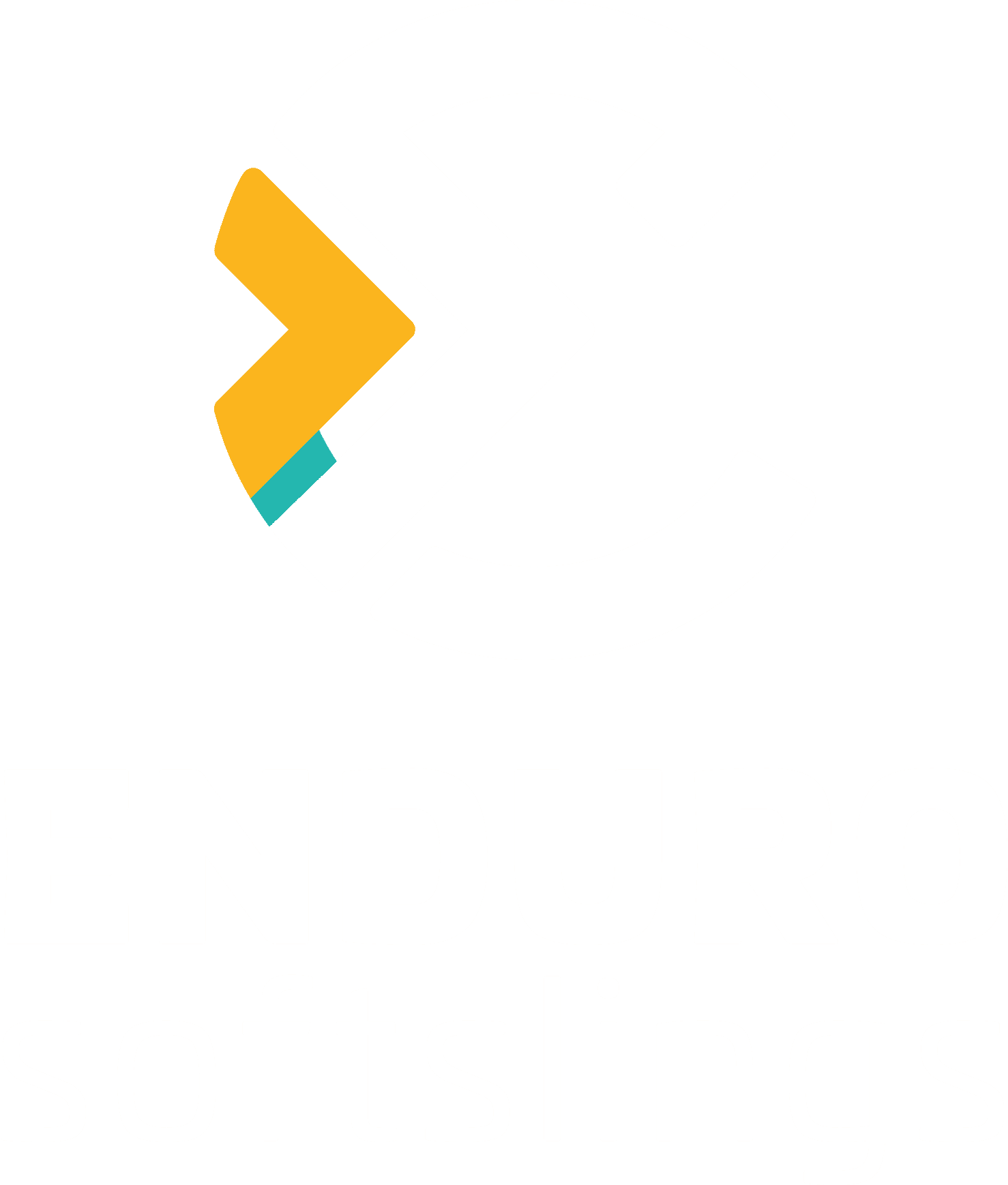
- +31 (0) 229 22 00 14
- info@softslings.com
-
Wieder 23a 1648 GA De GoornNederland
- Follow us on Linkedin
Last years the use of high performance synthetic slings is gaining popularity. One of the properties to this product is its very low elasticity. Will the design factors that were developed for steel rigging hold for the new generation lifting material? In this white we will zoom into the case, determine the problems and give recommendations to designers and engineers to avoid potential unsafe situations.
Current sling tension calculations are typically considering exact sling lengths. Due to manufacturing tolerances however, in real life one should take into account a certain mismatch in this length. Especially in lifts with 4 slings to 1 lifting point, different sling lengths will result in different load in each sling. Obviously the shortest sling will hold a larger load than the longtest. Elasticity in material will compensate for this effect as the shortest sling will stretch and distribute more of its load towards the other 3 slings in the rigging, but in material with low elasticity this effect is limited.
In order to deal with this uncertainty, suppliers are requested to manufacture their slings in so called ‘matched pairs’. This term has multiple possible definitions but mostly it refers to an item-to-tem length difference of max 0,5 times the sling diameter. This way the tolerance is somehow controllable, but the bigger the loads(and so the bigger the sling diameter), the larger the allowable length difference may be.
To compensate for this difference in length engineers multiply the minimal required breaking load with a safety factor of typical 1.25, this is called the Skew-load-factor (SKL). This factor is totally arbitrary and nowadays implemented the same way for every kind of material, no matter if it is polyester, HMPE or steel.
When lifting a box on 4 equal lifting points. Assuming a CoG that lays exactly in the center of the box. In ideal situation all 4 slings will take an equal load. But imagine 4 slings all out of the same production batch, matched pair ad so all within 0,5x the diameter from each other. Worst case scenario two opposite corners have the slings with a short length on the lower end of the tolerance. And the two other slings have a tolerance on upper end of the tolerance.
The SLF of 1.25 now compensate for a difference in load of max 125% per sling. So if in ideal situation both pairs take 50% of the load, worst case 62,5%/37,5% is still allowed.
Now if we take this theory in real case, and use 4 HMPE soft sling of 10.000mm with a diameter of 200mm. The max allowable length tolerance according to the matched pair definition is 100mm. Without going becoming too technical we can assume that a sling will stretch 0,5% during normal use and 1% on 2 times the Working load limit (WLL). If in this case the 2 opposite slings are both short (9.900mm) and the others are 10.000mm. Two slings will pickup all load while the other 2 barely touch the hardware. A SKL-factor of 2 should be applicable instead of 1.25.
Increasing the safety factors can be seen as treating symptoms. In fact solving the underlying problem might be far more effective. This will be decreasing allowable length differences, but at least detaching it from the diameter of the sling, as the length of the sling is a far more efficient parameter to work with. Beside that, be aware that in fact SKL-factors can better be determined per project/rigging instead of following the standard regulated factor of 1.25, taking into account the length of the actual hardware used.
Privacy | Disclaimer | Terms and conditions | ©Enduro Softslings